Уважаемые клиенты, с 01.01.2024г. мы прекращаем принимать инструменты BOSCH в платный ремонт
Типы изделий:
|
Диагностика и анализ неисправностей: Пила цепная бензиновая
Коленвал, искривление Развернуть ▼
|
Такая неисправность как искривление вала происходит по причине нарушения условий эксплуатации. За редким исключением это может быть заводской дефект. И то, это касается новых, еще не использовавшихся устройств.
Как это происходит? Во время работы цепь сильно нагревается и из-за температурного расширения начинает удлиняться (Рис.1). Что бы избежать сваливания цепи с шины, клиент вынужден подтягивать цепь до функционального положения. Заканчивая работу, оператор обязан отпустить цепь в исходное состояние.
В противном случае, если этого не сделано, происходит следующее. Цепь при остывании начинает возвращаться в исходное состояние, т.е. сжиматься. Усилия при этом присутствуют довольно значительные. Вся нагрузка, через опору подшипника, передается на хвостовик коленвала (Рис.2_А). В результате поломка происходит там где это было легче сделать. Либо
гнется хвостовик коленвала (Рис.2_В), разрушается или повреждается подшипник, разбивается посадочное место под подшипник, либо цепь вытягивается и растягивается на столько, что в конце концов рвется.
Искривление коленвала легко проверить с помощью индикаторной головки (Рис.3). По итогу можно сказать следующее, что искривление коленвала, за исключением случая оговоренного в начале статьи, относится к негарантийным случаям. И повреждения, связанные с этой неисправностью, являются результатом невнимательности пользователя. Открыть в новой вкладке
|
Двигатель 2-х тактный, первичная диагностика ''на слух'' Развернуть ▼
|
По характеру работы двигателя можно предварительно определить проблему. Важно понимать как это работает.
~~ Запустили двигатель, холостые не держит или неустойчивы, на газу работает без проблем.
Вопрос к байпасу карбюратора. В более ранней статье "Карбюратор для любознательных. Для чего ''дырочки'' в диффузоре" описывалось смысловое значение жиклеров холостого хода. На холостом ходу именно они отвечают за работу двигателя. При засоренных каналах холостой ход может даже присутствовать, но при нажатии на газ начинают падать обороты и двигатель глохнет. Это происходит в тот момент когда дроссельная заслонка приоткрыта, начинает подаваться дополнительный воздух, а главный топливный жиклер еще не вступил в работу. На Рис.1_GIF показан такой момент (моргает красным). И если удалось проскочить провал (быстренько схватить ручку газа и нажать на нее), то в дальнейшем в работу вступает главный жиклер и производительность жиклеров холостого хода игнорируется (большая разница в топливоподаче).
~~ Двигатель запустили, холостой нормальный, на газу либо не набирает обороты, либо совсем глохнет - вариантов несколько.
1. забит топливный фильтр в баке (всасывающая головка), менять даже если внешне похож на чистый.
2. неисправность в главном топливном жиклере (Рис.2) или в забитых каналах обеспечивающих подачу топлива к жиклеру. Демонтировать его можно аккуратно выбив латунной выколоткой (Рис._3). Устройство жиклера понятно из Рис.4. Через сквозное боковое отверстие топливо подается в карбюратор через обратный клапан.
~~ У работающего двигателя на холостых плавают обороты, на газу так же наблюдается неравномерность оборотов. Наиболее вероятная причина негерметичность двигателя по любым узлам с уплотнениями.
1. Сальники коленвала. Если они старые (укорчевшие), поврежденные либо криво установленные будет происходить подсос воздуха и как следствие дополнительная (не предусмотренная) добавка воздуха к уже готовой топливной смеси.
2. Поврежденные прокладки между карбюратором, соединительным коленом, цилиндром.
3. Поврежденный топливный шланг.
~~ Двигатель после запуска работает около 10 мин., затем глохнет и не запускается. Возможная причина - неисправность системы вентиляции бака (сапун). Происходит следующее. При работе двигателя объем выработанного топлива должен замещаться таким же объемом воздуха, который поступает в бак через сапун. Если он не работает, к примеру забит мусором, то в баке будет создаваться разрежение, которое будет препятствовать поступлению топлива в карбюратор. Принцип проверки прост. Как только двигатель заглохнет нужно открутить крышку топливного бака. Если будет слышно легкое шипение воздуха, значит в баке пониженное давление и дело определенно в сапуне. Поможет чистка или замена. Сам клапан может быть установлен как отдельно, так и интегрирован в пробку топливного бака.
Пробка с встроенным клапаном, ее устройство и принцип работы.
На Рис.5 детали пробки. (А)- сама пробка, (В)- уплотнительная прокладка, (С)- корпус сапуна, (D)- сапун, (Е)- ограничитель от выпадения пробки. В данном случае нас интересует сам клапан-сапун (Рис.6). Выполнен он по примеру ниппеля (стрелкой показаны сомкнутые половинки проходного канала). Демонтаж заключается в снятии плоским предметом, типа отвертки, ограничителя (Рис.5_Е).
На Рис.7 красной стрелкой показан путь воздуха в бак.
Еще очень много может сказать о работе двигателя свеча зажигания. Подробно об этом в статье "Кратко о свечах зажигания" http://remont.tools.by/diagnostics/view/1551960047.
Ну и конечно настройка карбюратора (при условии исправности всех перечисленных выше узлов). Статьи "Карбюратор настройка" http://remont.tools.by/diagnostics/view/1583157826, "Карбюратор настройка - нюансы" http://remont.tools.by/diagnostics/view/1583412753. Открыть в новой вкладке
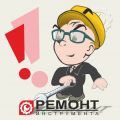 Лого 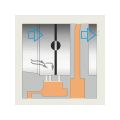 Рис. 1_GIF 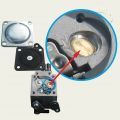 Рис. 2 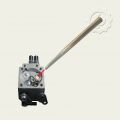 Рис. 3 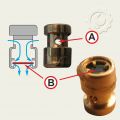 Рис. 4 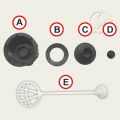 Рис. 5 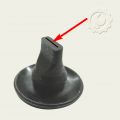 Рис. 6 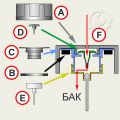 Рис. 7
|
Залегание колец Развернуть ▼
|
Залегание колец, как один из опасных повреждений двигателя. Из-за чего происходит и чем это опасно?
Основные причины образования нагара это неподходящее масло, добавляемое к топливной смеси и работа двигателя на пониженных оборотах (Рис.1).
В первом случае масло не соответствует температурному режиму и просто пригорает, накапливаясь в камере сгорания и в кольцевых углублениях в поршне (Рис.2).
На Рис.3 показан процесс залегания кольца. Красными зонами показаны места образования нагара (Рис.3_А). При разогретом двигателе поршень расширяясь, прижимается к стенкам цилиндра. Кольца при этом утапливаются в поршневые углубления (Рис.3_В). Охлаждаясь, поршень сжимается и кольца должны выйти из углублений. Но при достаточно сильной закоксованности, нагар не позволяет это сделать и кольца остаются зажатыми внутри поршневых углублений (Рис.3_С). Получилось залегание колец. При попытке дальнейшей работы, избыточная часть нагара отрывается и попадает между поршнем и стенками цилиндра с образованием последующих задиров.
Во втором случае (низкие обороты двигателя) происходит неполное сгорание топливной смеси. В результате масло, как медленнее испаряемая часть топливной смеси, в избыточном количестве прогорает в камере сгорания. Не происходит самоочищения зоны горения. Накапливается нагар с закоксовыванием. А дальше происходит тоже, о чем говорилось выше.
Дополнительно следует отметить следующее. Нагар может накапливаться до определенного момента, не вызывая залегания колец. И при избыточном его количестве, отрывается и попадает между стенками поршня и цилиндра в районе перепускных окон. По своему составу нагар имеет очень твердую структуру схожую со стеклом. Такие частицы становятся причиной сильных задиров с частичным смещением кромок поршня и блокируя кольца (Рис.4).
Случай не является гарантийным и относится к эксплуатационным повреждениям. Открыть в новой вкладке
|
Масляный привод и насос, замена (ECO_CSP-165) Развернуть ▼
|
Несмотря на то, что масляный привод и насос в бензопиле CSP-165 внешне и по посадочным параметрам схож с аналогичными деталями к бензопилам типа CSP-153, CSP-164, имеет определеное отличие - это шаг резьбы червяка привода и соответственно насоса. По этому, при замене какой-то из этих деталей, следует учитывать этот факт и менять узел в комплекте (привод + насос + цепной барабан). Открыть в новой вкладке
|
Поршень. Какой стороной устанавливать? Развернуть ▼
|
Иногда возникает вопрос, какой стороной установить поршень? Где у него передняя, а где задняя части? Попробуем разобраться.
Как правило, осевое положение пальца поршня несколько смещено в одну из сторон относительно оси самого поршня. На слабонагруженной технике встречаются поршни с пальцами, расположенными на одной оси с осью поршня. В этом случае нет разницы какой стороной устанавливать поршень. Для поршней со смещенным пальцем разница есть и о ней поговорим подробнее.
На (Рис.1_А) ось вращения коленвала, (Рис.1_В) ось вращения шатуна относительно коленвала. Во время работы двигателя (красной стрелкой показано направление вращения коленвала) шатун постоянно находится под некоторым углом к оси цилиндра, причем этот угол постоянно изменяется. Поэтому сила, приложенная к поршневому пальцу, раскладывается на две. Эти силы назовем Fшатуна (Fш) и Fпоршня (Fп) (Рис.2). В результате действия этих сил возникает третья сила, воздействующая на поршень и направленная перпендикулярно оси цилиндра. Назовем ее Fрезультирующая (Fрез.). Чем больше силы Fш и Fп, тем больше будет сила Fрез.
В ВМТ и НМТ вектора Fш и Fп складываются и Fрез. в этом случае будет равна нулю (Рис.3).
После прохождения ВМТ происходит вспышка топливной смеси и поршень перекладывается, т.к. меняется направление силы вектора шатуна (Fш) (Рис._4_А). И в этом цикле сила эта намного больше той силы, что была при сжатии. Если верить справочникам, то боковая сила, прижимающая поршень к стенке цилиндра приблизительно равна 10% — 12% процентов, от силы, действующей в направлении оси цилиндра. У автомобиля это около нескольких сотен килограмм. Из-за скоротечности процесса такое перекладывание поршня можно сравнить с ударом.
Для уменьшения силы удара, при перекладке поршня, ось поршневого пальца (вернее ось отверстия в бобышках поршня под поршневой палец) смещена в сторону основной упорной поверхности, т.е. вперед по направлению движения газов (Рис._5). Дополнительно на днище поршня ставится отметка (Рис.6_А).
По итогу нужно запомнить следующее. Метка на поршне всегда стоит со стороны где палец ближе к стенке поршня (Рис.7_А) и направлена должна быть против хода вращения коленвала (Рис.7_В).
Возникли вопросы, пришлось дополнить статью и разложить более подробно.
На Рис.8 поршни с центральным расположением пальца (слева) и со смещенным (справа).
Вертикальная сила (Рис.8_1), действующая на поршень, раскладывается на две разнонаправленные (Рис.8_2) и (Рис.8_3). Это происходит потому, что вектор шатуна (Рис.8_2) смещен относительно вертикали и направлен на точку опоры шатуна и шейки коленвала. Эти силы прижимают поршень к одной из сторон цилиндра (Рис.8_4). В данном примере вращение коленвала против часовой стрелки.
По мере вращения коленвала шатун принимает противоположные углонаправленные положения, заставляя поршень перекладываться с одной стороны на другую. При скоротечности процесса такие перекладывания сродни ударам. Все эти силы и при цикле сжатия, и при цикле вспышки. Но вертикальная сила, действующая на поршень при вспышке, гораздо больше этой же силы при цикле сжатия. По-этому и сила прижатия к стенке цилиндра при вспышке будет больше. Такое явление негативно сказывается на износостойкости и общей работе двигателя. Чтобы уменьшить такие нагрузки палец смещается относительно оси поршня. Такое смещение обычно с пределах 1-2,5 мм. Теперь о том что происходит.
Если палец расположен по центру и совпадает с осью поршня, то вертикальная сила действующая на поршень будет поровну распределена как на переднюю часть дна поршня (Рис.9_1), так и на заднюю (Рис.9_2). При смещении пальца вертикальная сила будет распределена на дно поршня не равномерно. Это можно с некоторой натяжкой сравнить с коромыслом, где точка переваливания будет на оси поршневого пальца. И чтобы при вспышке топлива уменьшить силу прижатия поршня к стенке цилиндра смещают ось пальца относительно оси поршня против хода вращения коленвала и по ходу отработанных газов.
Получается что на переднюю часть дна поршня приходится меньшая сила (Рис.9_5) чем на заднюю (Рис.9_4) и сила прижатия при этом соответственно уменьшится (Рис.9_6) против варианта с центральным расположением пальца (Рис.9_3). Это происходит потому, что бОльшая сила (Рис.9_4), частично преодолевая меньшую силу (Рис.9_5) пытается удержать поршень в вертикальном положении и значительно снимает нагрузку давления на стенку цилиндра (Рис.9_6) Открыть в новой вкладке
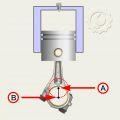 Рис.1 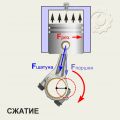 Рис.2 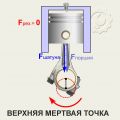 Рис.3 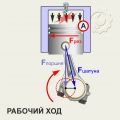 Рис.4 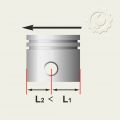 Рис.5 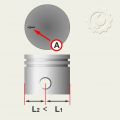 Рис.6 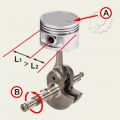 Рис.7 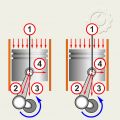 Рис.8 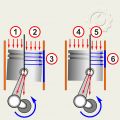 Рис.9
|
Карбюратор настройка (2-х тактные двигатели) Развернуть ▼
|
Существует несколько вариантов исполнения безпоплавковых карбюраторов. Некоторые модели карбюраторов, в целях удешевления товара, исполнены в нерегулируемом варианте. Такие карбюраторы, в случаях каких-нибудь неисправностей, просто меняются на новый. В нашей статье мы рассмотрим карбюратор, который поддается полной регулировке как по качеству смеси, по ее количеству, так и по режиму холостого хода (ХХ).
Такие карбюраторы имеют три регулировочных винта. Винт качества смеси (Рис.1_А), обозначается буквой "L". Он расположен всегда ближе к цилиндру. Винт количества смеси (Рис.1_В) или винт максимальных оборотов, обозначается буквой "H". И винт регулировки холостого хода (Рис.1_С). На Рис.1_D - условно обозначен главный жиклер.
В первую очередь необходимо настроить качество смеси. Идеальным соотношением воздуха к топливу (по весу) 14,7/1 (14,7кг воздуха к 1кг топлива). Такое соотношение называют стехиометрической. При таком соотношении коэффициент избытка воздуха равен единице (обозначается буквой лямбда), т.е. лямбда равна единице.
Если вращать винт в сторону откручивания, то этим самым мы, добавляя топливо, обогащаем смесь и лямбда становится меньше единицы (лямбда - соотношение воздуха к топливу, а не наоборот). На Рис.2_GIF понятна закономерность обогащения смеси и реакция двигателя.
Вращение винта в обратную сторону приводит к противоположному результату (Рис.3_GIF). Смесь обедняется и коэффициент избытка воздуха (лямбда) становится больше (много воздуха - мало топлива).
В обоих случаях обороты двигателя падают. Наша задача добиться максимальных оборотов двигателя, найдя такое положение винта качества смеси, при котором это требование будет выполняться (Рис.4_GIF).
После того как мы выставили максимальные обороты двигателя, винтом холостого хода (подпирает дроссельную заслонку, может обозначаться LD) (Рис.1_С) добиваемся такого положения при котором обороты двигателя будут на 300 об/мин больше нормальных оборотов холостого хода. В нашем случае ХХ 2800 об/мин. Мы докручиваем до 3100 об/мин (Рис.5_GIF).
Возвращаемся к винту качества смеси "L" (Рис.1_А) и вращаем в сторону ОТКРУЧИВАНИЯ (встречаются карбюраторы с левой резьбой). При этом обороты начнут падать. Доводим обороты двигателя до нужных нам 2800 об/мин (Рис.6_GIF).
Завершаем настройку карбюратора винтом количества смеси "Н" (Рис.1_В). Выжимаем полный газ и по тахометру выставляем необходимое количество максимальных оборотов.
Если ориентироваться "на слух", то придется ориентироваться по реакции двигателя. Если при резком нажатии на газ происходит провал (двигатель как бы "душится"), то это означает обеднение топлива в переходный момент (винтом "Н" добавить, открутить). Если максимальные обороты недостаточны, двигатель не набирает нужные обороты - смесь богатая. Винт "Н" закрутить для уменьшения подачи топлива. Открыть в новой вкладке
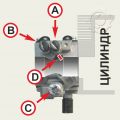 Рис.1 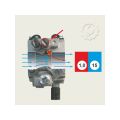 Рис.1_GIF 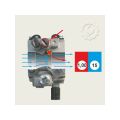 Рис.2_GIF 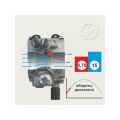 Рис.3_GIF 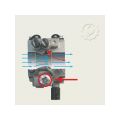 Рис.4_GIF 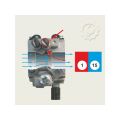 Рис.5_GIF
|
Цепи, заточка (цепные пилы) Развернуть ▼
|
Эта статья для тех у кого-то возникнет необходимость правильно либо заточить цепь, либо объяснить клиенту как грамотно это сделать. Если подобная задача стоит в условиях сервисного центра и заточки цепей носят не единичный характер, то лучший вариант это приобретение заточного станка (Рис.1).
Заточка цепи не совсем простая задача. Здесь надо учитывать одновременно несколько углов положения заточного инструмента, а заточка разно направленных зубьев должна быть произведена под одинаковыми углами. В противном случае цепь постоянно будет уходить в сторону, а шина изнашиваться неравномерно.
Для заточки лезвия режущего зуба понадобится специальный круглый напильник (Рис.2). Эти напильники разделяются по размерам. Диаметр напильника напрямую зависит от шага цепи.
• Шаг 1/4″ – диаметр 4,0 мм;
• Шаг 0,325″ — 4,8 мм;
• Шаг 3/8″ — 5,2 мм;
• Шаг 0,404″ — 5,5 мм.
Выше было сказано о не совсем простой задаче при заточке и вот в чем она заключается. Цепь, во время заточки при помощи напильника, должна быть натянута. Затачиваемый зуб, должен располагаться примерно посредине шины, это необходимо для удобства проведения работ. В процессе заточки нужно продвигать цепь по шине, не забывая при этом каждый раз устанавливать тормоз в рабочее положение. Напильник следует держать перпендикулярно вертикальной плоскости шины под углом 90 градусов (Рис.3) и одновременно выдерживать угол в 30 градусов относительно перпендикулярной линии к линии шины (Рис.4_А). В большинстве своем на режущем зубе имеется сервисная метка. Она указывает направление заточки и предел до которого можно точить цепь (Рис.5). Заточка цепи производится движениями напильника изнутри зуба наружу.
Значительно упростить задачу помогут несложные приспособления. Для правильного угла заточки используют специальные шаблоны (Рис.6). Пример использования на Рис.7_А. Шину необходимо лишить ненужной подвижности. Для этого можно воспользоваться способом с подкладыванием между цепью и шиной штатного свечного ключа (Рис.7_В), либо воспользоваться струбциной (Рис.8).
Стачиваясь зуб как бы уходит виз. Это обусловлено конструкцией режущего зуба, задняя часть режущей полки ниже режущей ее части. Соответственно количество захватываемой древесины уменьшается, что существенно сказывается на производительности. За глубину реза отвечает ограничительный зуб (Рис.9). После заточки режущей части необходимо подточить и ограничительный зуб. Он должен быть утоплен на 0,65 мм. Для этого может пригодиться еще один шаблон (Рис.10) и плоский напильник (Рис.11). Приложив шаблон на цепь можно заметить выступающий ограничитель (Рис.12). Плоским напильником его следует спилить вровень с шаблоном (Рис.13).
(!!!) Работу по заточке цепи, нужно обязательно проводить с использованием перчаток из грубого материала. В противном случае можно достаточно легко себя травмировать, т.к. рабочая поверхность зубьев очень острая.
Углы заточки цепей подробно оговорены в предыдущей статье "Углы заточки пильных цепей", https://remont.tools.by/diagnostics/view/1652518345 Открыть в новой вкладке
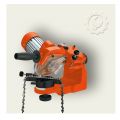 Рис.1 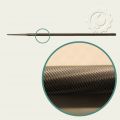 Рис.2 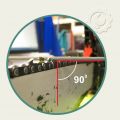 Рис.3 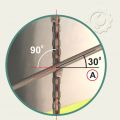 Рис.4 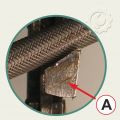 Рис.5 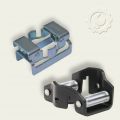 Рис.6 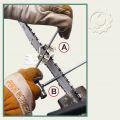 Рис.7 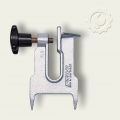 Рис.8 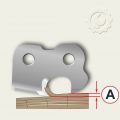 Рис.9 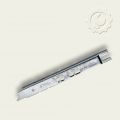 Рис.10 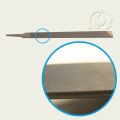 Рис.11 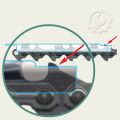 Рис.12 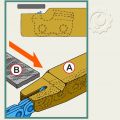 Рис.13
|
Подшипники аналоги (ГОСТ - международная система) Развернуть ▼
|
В последнее время мы привыкли к международной системе обозначений подшипников, но иногда встречаются обозначения по ГОСТу (отечественные подшипники). Здесь приведена таблица наиболее встречающихся в использовании у нас подшипников однорядных шариковых радиальных с обозначением по ГОСТу и их аналогов по международной маркировке. Нас интересуют в первую очередь сравнительные обозначения и основные размеры: наружный диаметр (Рис.1_D,Рис.4_D), внутренний диаметр (Рис.1_d,Рис.4_d) и высота подшипника (Рис.1_B,Рис.4_B).
Вначале оговоримся по маркировке ГОСТ. Подшипники могут быть открытыми, закрытыми с одной стороны и закрытыми с двух сторон защитной крышкой. Крышки могут быть металлические (Рис.1_А) и резинометаллические(Рис.2_А). Резинометаллические крышки лучше сохраняют подшипник то попадания грязи и пыли. Металлические крышки лучше переносят высокие обороты. Для примера возьмем подшипник 608(по международному стандарту), его аналог по ГОСТ (Рис.3). Последние 2 цифры (Рис.3_желтая зона) это основной тип подшипника 22-наружный диаметр_D, 8-внутренний диаметр_d, 7-высота подшипника_B. Под основной тип подшипника зарезервированы 4 последних знака. Пятая цифра сзади (Рис.3_красная зона)- количество защитных крышек, где 6-это одна крышка, 8-подшипник имеет крышки с обеих сторон. Перед 6-кой или 8-кой единица (Рис.3_зеленая зона) говорит о том, что крышки резинометаллические. Отсутствие знака - металлические. Как пример: 180018 (ГОСТ), подшипник типоразмера 22х8х7 защищен с двух сторон крышками из резинометаллического материала или 80018 (ГОСТ) подшипник 22х8х7 с двумя резинометаллическими крышками.
Обозначение защитных крышек по международному стандарту (ISO):
* отсутствие после цифр суффикса - открытый (608)
* Z-одна металлическая крышка (608-Z)
* 2Z-металлические крышки с двух сторон (608-2Z)
* RS- одна резинометаллическая крышка (608-RS)
* 2RS-резинометаллические крышки с двух сторон (608-2RS).
СРАВНИТЕЛЬНАЯ ТАБЛИЦА АНАЛОГОВ
ISO________ГОСТ________D-d-B________max об/мин
6000_______100________26-10-8__________30000
6001_______101________28-12-8__________32000
6002_______102________32-15-9__________28000
6003_______103________35-17-10_________24000
6004_______104________42-20-12_________20000
6005_______105________47-25-12_________18000
6008_______108________68-40-15_________12000
6009_______109________75-45-16_________11000
607_________17________19-7-6___________34000
608_________18________22-8-7___________32000
609_________19________24-9-7___________30000
61804____1000804______32-20-7__________22000
_6804____1000804______32-20-7__________22000
61806____1000806______42-30-7__________18000
_6806____1000806______42-30-7__________18000
6200_______200________30-10-9__________30000
6201_______201________32-12-10_________22000
6202_______202________35-15-11_________19000
6203_______203________40-17-12_________17000
6204_______204________47-20-14_________15000
6205_______205________52-25-15_________12000
6206_______206________62-30-16_________10000
625_________25_________16-5-5__________36000
626_________26_________19-6-6__________32000
627_________27_________22-7-7__________30000
628_________28_________24-8-8__________31000
629_________29_________26-9-8__________26000
6300_______300________35-10-11_________26000
6301_______301________37-12-12_________26000
6302_______302________42-15-13_________20000
6306_______306________72-30-19__________9000
6307_______307________80-35-21__________8500
6308_______308________90-40-23__________7500
6309_______309_______100-45-25__________8000
6900_____1000900______22-10-6__________36000
6902_____1000902______28-15-7__________28000
6905_____1000905______42-25-9__________18000
696______1000096_______15-6-5__________45000
697______1000097_______17-7-5__________43000
698______1000098_______19-8-6__________40000
30303_____7303_________47-17-15_________8500 Открыть в новой вкладке
|
Карбюратор диагностика, ремонт Развернуть ▼
|
Статья касается карбюраторов для 2-ух тактных двигателей общего типа (Рис.1), без праймера, самовзвода и пр. дополнений.
Откручиваем винт (Рис.2_А). Сняв крышку, под ней видим прокладку (Рис.2_В) и мембрану клапанов (Рис.2_С). С другой стороны карбюратора откручиваем 4 винта и снимаем крышку (Рис.3_А). Под ней находятся дозирующая игла, жиклеры и мембрана управления иглой. Дозирующая игла приводится в действие целым механизмом, который состоит из коромысла (Рис.4_А), оси (Рис.4_В), самой иглы (Рис.4_С) и фиксирующего винта (Рис.4_D). Под коромыслом находится пружинка, которая через коромысло прижимает иглу к седлу, перекрывая топливный канал.
Открутив винт (Рис.4_D), демонтируем коромысло (Рис.5_А) с осью (Рис.5_В). Убеждаемся в свободном вращении коромысла на оси. При удержании рукой за ось, коромысло должно свободно под своим весом проворачиваться по оси и опускаться вниз.
Затем проверяем свободное перемещение иглы в канале. Взявшись за иглу пинцетом, отпускаем ее в канал (Рис.7). Она так же под своим весом должна беспрепятственно падать вниз. После этих проверок и обратного монтажа механизма дозирующей иглы проверяем уровень относительно коромысла и корпуса карбюратора (Рис.8). Коромысло не должно выступать или глубоко сидеть относительно краев ниши в корпусе. Т.е. быть почти вровень с краями.
В конце, с обратной стороны карбюратора, проверяем фильтрующую сетку (Рис.9). Она должна быть абсолютно чистой. Если устройство побыло в эксплуатации, то лучше ее заменить. Открыть в новой вкладке
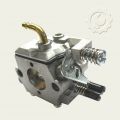 Рис.1 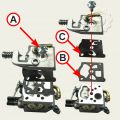 Рис.2 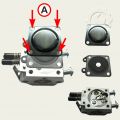 Рис.3 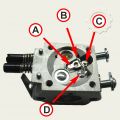 Рис.4 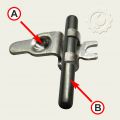 Рис.5 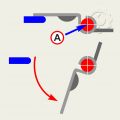 Рис.6 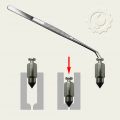 Рис.7 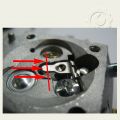 Рис.8 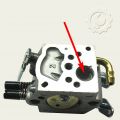 Рис.9
|
Кольца поршневые_завышен размер Развернуть ▼
|
Обнаружилось неприятное явление с ЦПГ для бензопил. Это касается поршневых групп диаметром 45мм. ЦПГ поставляются в сборе и кольца, которые лежат в комплекте, имеют завышенный размер и не входят в цилиндр. Тепловой зазор колец в замке должен быть в районе 0,3мм (Рис.1). Полученная партия ЦПГ, в некоторых случаях, имеет комплектные кольца, которые невозможно установить в цилиндр и становятся с нахлестом (Рис.2). При ремонте следует иметь ввиду этот факт и заранее проверять размерность колец, поместив их в цилиндр. Сделав это до монтажа поршня и цилиндра можно сэкономить кучу рабочего времени и нервов. Открыть в новой вкладке
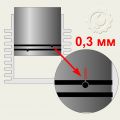 Рис.1 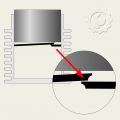 Рис.2
|
Прогар поршня Развернуть ▼
|
Иногда в ремонт потупают двигатели с прогоревшим поршнем. В чем может быть проблема? Есть две причины возникновения такого повреждения.
Бывают поршни прогоревшие по боковой стенке (Рис.1_А) и по днищу (Рис.1_В).
В первом случае причиной может быть некачественное масло в топливной смеси, слишком богатая смесь либо работа в режиме постоянной перегрузки двигателя. Т.е. причины, приводящие к закоксовыванию поршня с залеганием поршневых колец. В двигателях внутреннего сгорания предусмотрен температурный зазор поршня и поршневых колец. При работе двигателя поршень, переходя верхнюю мертвую точку, как бы переваливается в пределах теплового зазора(Рис.2). Образовавшийся зазор, компенсируют поршневые кольца, обеспечивая компрессию в камере сгорания (Рис.2_А). Если же кольца залегли, то в получившийся зазор прорывается газ от сгорания топливной смеси (Рис.3_А). В результате боковая стенка поршня получает мощный тепловой удар. Здесь сказывается большая скорость разогрева и слабое охлаждение поршня в этой зоне, т.к. находится со стороны выхода выхлопных газов. Повреждение поршня, как правило, имеет клиновидную форму (Рис.4_А). Края поврежденного участка имеет ярко выраженные следы оплавления.
Во втором случае это может быть детонация. В этом случае повреждения будут иметь вид механического повреждения и местом разрушения будет дно поршня (Рис.5). Т.е. по краям разлома будет видна кристаллическая структура металла без явных следов оплавления. Что такое детонация и чем она может быть вызвана?
Энциклопедическая формулировка: "Детонация — режим горения, при котором по веществу распространяется ударная волна, инициирующая химические реакции горения. Иногда формулируют как «сгорание во фронте ударной волны».
При нормальной работе двигателя скорость распространения фронта пламени в момент вспышки топлива обычно не более 50 м/сек. При детонации - скорость сгорания топлива происходит со сверхзвуковой скоростью и может превышать скорость звука в несколько раз (скорость звука 330 м/сек). При такой скорости горения появляется ударная волна с выделением большого количества тепла, что и приводит к разрушению поршня.
Основной причиной вызывающей детонацию является применение топлива с низкооктановым числом. Можно возразить, мол где сейчас можно найти низкооктановый бензин? Но тут есть нюанс. В основе любого бензина есть базовый бензин, который изначально получается после ректификации нефти. Он как правило имеет низкое октановое число и составляет около 65 ед. Есть и другие варианты с применением более современных технологий, но это все равно будет бензин с числом около 74-76 ед. Дальше вступают в процесс антидетонационные присадки. Эти присадки имеют свойство улетучиваться. Все зависит от условий хранения. Плюс к этому вы не можете знать насколько свежий бензин был на заправке. Более подробную информацию по этому вопросу можно найти в интернете. Можно только сказать следующее, при неблагоприятном стечении обстоятельств с условиями хранения можно через 3-4 недели получить низкооктановый бензин с выше сказанными неприятностями.
Похожие повреждения, такие как на Рис.5 могут случиться из-за калильного зажигания. Это и некачественный бензин с какими-нибудь особыми присадками и конечно свечи зажигания с неправильно подобранным калильным числом. На слишком "холодных" свечах может образовываться нагар, а слишком "горячие" могут способствовать калильному зажиганию. Т.е. вспышка топлива будет происходить раньше положенного времени, до выхода поршня в ВМТ.
Открыть в новой вкладке
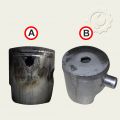 Рис.1 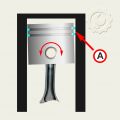 Рис.2 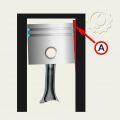 Рис.3 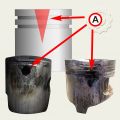 Рис.4 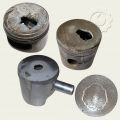 Рис.5
|
Стартер ErgoStart принцип работы Развернуть ▼
|
Стартера с обычной системой и системой ErgoStart принципиально отличаются друг от друга не только конструктивным исполнением, но и приемом запуска двигателя. Очень часто в устройствах, где используется система ErgoStart, клиенты зачастую совершают одну и ту же ошибку, пытаясь применять приемы запуска как с обычными стартерами. Разберем подробнее.
ErgoStart - это запатентованная в 2003 году инновационная технология компании STIHL. Подобная технология значительно облегчает запуск двигателя и не требует от оператора необходимость дергать за ручку стартера. Как это работает? Между стартерной катушкой и коленчатым валом размещена пружина с двумя поводками (Рис.1_А), которая натягивается при плавном вытягивании тросика. В камере сгорания находится воздух, который сжимаясь на каком-то этапе препятствует проворачиванию коленвала. Пружина, сжимаясь, аккумулирует энергию пружины (Рис.2_А). Затем, в какой-то момент усилие пружины преодолевает сопротивление воздушной подушки в камере сгорания и вся энергия, накопленная пружиной, одномоментно передается на коленвал, запуская двигатель (Рис.3). Этим предотвращаются повышенные нагрузки, которые возникают при рывках. Пружина передает коленчатому валу энергию, конвертирует ее в движение, чем обеспечивает правильный безопасный запуск мотора. Оператору нужно всего лишь потянуть за тросик без резких рывков и больших усилий.
На Рис.4 показан сравнительный график запуска двигателя обычным стартером и стартером ErgoStart. График взят с официального сайта компании STIHL. Вертикальные столбцы - это количество тактов двигателя при вытягивании троса стартера. Как видно из графика при вытягивании троса с обычным стартером происходят рывки на каждом такте двигателя, что и передается на руку оператора, вынуждая его прилагать дополнительные усилия в виде резкого дергания на рукоятку стартера. С ErgoStart-ом это не происходит. Оператор плавно вытягивает трос и в какой-то момент происходит запуск двигателя.
Клиенту, который не знакомом с подобной конструкцией, следует объяснить что дергать за рукоятку стартера не только необязательно, но даже вредно для конструкции. Иногда по этой причине происходили поломки в виде повреждения пружины.
Открыть в новой вкладке
|
Задир ЦПГ, наиболее вероятные причины Развернуть ▼
|
Предварительная оценка повреждений - очень важный этап диагностики. Ошибочное предварительное мнение может сыграть ключевую роль в дальнейшей оценке причин неисправности. Механик может пойти по ложному пути рассуждений и в дальнейшем, подводя под свою первичную оценку, объяснять почему эти повреждения произошли, подтасовывая факты. Человек делает это не осознанно, просто в силу своих убеждений.
Перед нами двигатель с тепловым задиром ЦПГ. По характеру задира на поршне можно определить причины по которым произошло повреждение. Подача топлива и его сгорание происходит от впускного окна (Рис.1_А) до выпускного (Рис.1_В). Следовательно та часть поршня, которая находится к впускному окну всегда будет холоднее чем та, которое направлена к выпускному окну (Рис.2). Через впускное окно постоянно подается топливо, охлаждая эту часть поршня (Рис.2_А). После вспышки, отработанные горячие газы выбрасываются в выпускное окно, разогревая эту часть поршня (Рис.2_В).
Если двигатель перегревается и выходит за температурные расчетные нормы, то происходит локальный срыв масляной пленки и как результат задир. В случаях перегрева задир начинается с самой горячей точки - выпускное окно (почему, говорилось выше). Если вы увидели локальный задир со стороны глушителя (Рис.3), то однозначно это тепловой задир. Задир по перегреву можно получить двумя способами. Ограничить охлаждение двигателя и бедная смесь. На тему бедной смеси есть сопутствующая статья на сайте "Кратко о двухтактных двигателях" http://remont.tools.by/diagnostics/view/1551959975. Отсутствие охлаждения двигателя может быть в случаях когда ребра цилиндра покрыты теплоизолирующей грязью или как в случаях с бензорезами гудроном (при резке асфальта).
Если есть такой же локальный задир со стороны впускного окна (Рис.4) это может свидетельствовать о том, что работали с грязным воздушным фильтром или вовсе без него. Посторонние частицы через впускное окно попадали в камеру сгорания, по пути повреждая поршень на входе.
Если же задир по всей окружности поршня и поршень при этом не имеет замасляности (сухой), это отсутствие смазывающего материала в топливе. Здесь задир начинается со стороны выпуска (Рис.5) и почти сразу распространяется по всей поверхности (Рис.6) как только поршень начнет расширяться и выбирать тепловые зазоры.
Остальные случаи можно отнести к визуально понятным, Рис.7 - обламывание стопорного или поршневого кольца, разрушение сепаратора подшипника коленвала либо попадание постороннего предмета через впускное окно. Здесь надо смотреть по обстоятельствам и внимательно осмотреть картер на наличие осколков и идентификации их. На Рис.8 - разрушение подшипника и характерные вмятины от его шариков. Открыть в новой вкладке
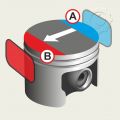 Рис.1 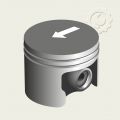 Рис.2 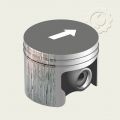 Рис.3 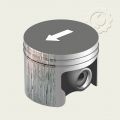 Рис.4 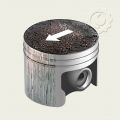 Рис.5 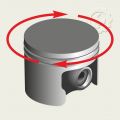 Рис.6 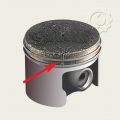 Рис.7 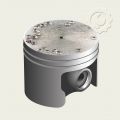 Рис.8
|
Некомплект GS-232 _ GS-282 Развернуть ▼
|
Обнаружены случаи некомплекта в бензопилах моделей GS-232 и GS-282. Отсутствует крепление воздушного фильтра.
В предыдущих моделях бензопил, таких как GS-231, GS-281 и пр., крепление воздушного фильтра осуществлялась внешней гайкой через прижатие крышкой фильтра (Рис.1_А). В моделях GS-232 и GS-282 крепление фильтра реализовано отдельным креплением ввиде барашкового винта и расположен он под крышкой фильтра (Рис.1_В).
Воздушный фильтр крепится барашковым винтом через шайбу (Рис.2). Вот их-то порой и нет в комплекте. Фильтр просто насажен на крепежную шпильку. Так же иногда отсутствует и прокладка между воздушным фильтром и корпусом (Рис.3). Барашковый винт с резьбой М5 и шайба в внутренним отверстием 5мм (Рис.4).
Возможно кому-то пригодятся размеры прокладки. В случае безвыходной ситуации, когда есть желание изготовить из подходящей резины. (Рис.5_А) размеры прокладки с указанием диаметров отверстий. (Рис.5_В) координатные размеры межосевых расстояний отверстий. Открыть в новой вкладке
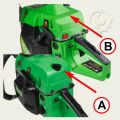 Рис.1 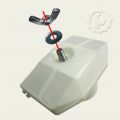 Рис.2 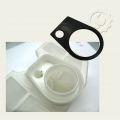 Рис.3 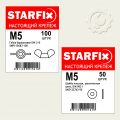 Рис.4 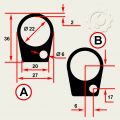 Рис.5
|
Углы заточки пильных цепей Развернуть ▼
|
Остро заточенная цепь обеспечивает эффективную, безопасную и точную работу цепной пилы. В этой статье речь об углах заточки.
Вначале о конструктивном исполнении режущего звена пильной цепи. Режущий зуб состоит из основания зуба (Рис.1_1), лопатки зуба (Рис.1_2), ограничителя глубины реза (Рис.1_3). Лопатка имеет вертикально расположенное торцевое лезвие (Рис.1_4) и спадающее подуглом назад верхнее лезвие (Рис.1_5), расположенное горизонтально.
В вертикальном направлении по срезу зуб (Рис.2_В) погружается на глубину до ограничителя (Рис.2_А). В горизонтальном направлении (Рис.3) дерево срезается боковой (вертикальной) частью зуба. Все режущие кромки должны иметь правильные углы заточки. От правильно заточенной цепи зависит не только точность выполняемой работы, но и значительно уменьшает нагрузку на двигатель.
Задний угол верхнего лезвия (наклон)(Рис.4). Спадающая под углом назад спинка зуба образует задний угол верхнего лезвия. Этот угол необходим для врезания верхнего лезвия в древесину и определен заводом изготовителем.
Задний угол торцевого лезвия (Рис.5). Суживающаяся назад лопатка зуба образует задний угол торцевого лезвия. Угол служит для бокового обрезания стружки и препятствует прихватыванию шины в дереве. Этот угол также остается неизменным и заточке не подлежит.
Передний угол (Рис.6). Кромка торцевого лезвия образует с поверхностью скольжения режущего зуба передний угол. В основной массе цепей этот угол составляет 85 градусов. Исключением являются специальные цепи - с победитовыми напайками (Rapid Duro) 65 градусов и для продольной распиловки 80 градусов.
Задний угол верхнего лезвия (скос)(Рис.7). Этот угол наиболее важен. Он должен быть, в зависимости от типа цепи, от 50 до 60 градусов, но специально его определять при заточке нет необходимости. При соблюдении остальных предписанных величин он должен получиться автоматически.
Угол заточки в плане (угол верхней кромки)(Рис.8). Угол заточки или угол в плане (вид сверху) получается измерением от верхней режущей кромки под прямым углом к направляющей шине цепи. В основной массе цепей этот угол составляет 30 градусов. Исключением являются цепи с победитовыми напайками (типа Rapid Duro) - 25 градусов и для продольной распиловки 10 градусов.
Расстояние ограничителя глубины (Рис.9). В большинстве используемых цепей этот размер равен 0,65 мм. Это цепи с шагом 1/4; 3/8; .325; Для цепей с шагом .404 требуется больший размер для ограничителя - 0,8 мм.
Кратко основные размеры:
* передний угол (Рис.6) - 85 градусов
* угол в плане (Рис.8) - 30 градусов
* ограничитель глубины (Рис.9) - 0,65 мм
Открыть в новой вкладке
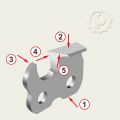 Рис.1 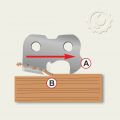 Рис.2 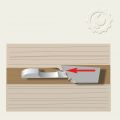 Рис.3 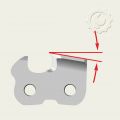 Рис.4 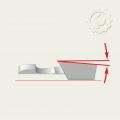 Рис.5 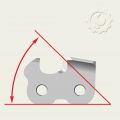 Рис.6 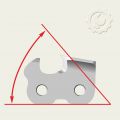 Рис.7 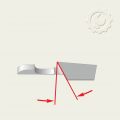 Рис.8 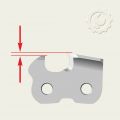 Рис.9
|
Притирание тормозной ленты (Вариант 1) Развернуть ▼
|
Притирание тормозной ленты о цепной барабан может происходить по двум причинам - это дефект крышки тормоза цепи и дефект самой тормозной ленты. Первая причина изложена в этой статье.
Неисправность, о которой пойдет речь, в последнее время приняло довольно массовый характер. У новых пил в большом количестве присутствует такой дефект как притирание тормозной ленты о цепной барабан. Причина - некачественное изготовление корпуса крышки тормоза цепи (Рис.1). Замена на новую крышку не помогает, на складе запчасти с таким же дефектом.
Притирание происходит по нижней части ленты (Рис.2). Если посмотреть внимательно на внутреннюю часть крышки, то заметим что уложеная тормозная лента в отпущенном состоянии не укладывается в окружность, а образует некоторый эллипс. Рис.3_А - фактическое положение ленты. Рис.3_В окружность, в которой теоретически должна находиться тормозная лента. В результате такого положения ленты, происходит ее притирание к цепному барабану (Рис.4_белая стрелка). Нижняя опора тормозной ленты, что является частью корпуса, не дает ленте лежать по окружности. Т.е. корпус выполнен с конструктивным дефектом геометрии.
Случай относится к гарантийным и изделие нуждается в замене, т.к. новые крышки имеют такой же дефект.
Негативные последствия такого притирания тормозной ленты о барабан на Рис.6. Начальная стадия оплавления (Рис.6_А), лента сдвинута для наглядности. Фатальное оплавление (Рис.6_В), тормозная лента снята.
P.S. Можно предложить вариант исправления дефекта путем удаления части корпуса (опорная нижняя часть под тормозную ленту) - Рис.5 Открыть в новой вкладке
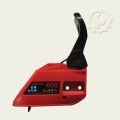 Рис.1 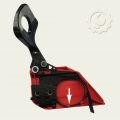 Рис.2 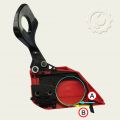 Рис.3  Рис.4 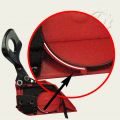 Рис.5 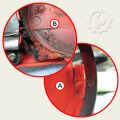 Рис.6
|
Притирание тормозной ленты (Вариант 2) Развернуть ▼
|
Второй вариант притирания тормозной цепи к цепному барабану отличается от предыдущего тем, что в данном случае неисправность касается не дефектного корпуса, а самой тормозной ленты.
В тормозную расстопоренную ленту должна вписываться окружность цепного барабана без какого-либо касания (Рис.1). В исправной крышке тормоза цепи лента лежит ровно и опирается на все ограничители корпуса крышки (Рис.2). Дефект можно обнаружить по опоре (Рис.3). На этом рисунке лента прилегает к опоре, что свидетельствует об исправном устройстве.
Если инструмент с дефектом, то лента, в этом месте, не будет прилегать (Рис.4). На Рис.5 показано в укрупненном плане, где хорошо заметен довольно большой зазор.
Причиной такой неисправности является плохая повторяемость при изготовлении тормозных лент. Как выяснилось, они имеют разную длину. При замерах лент (Рис.6) от точки (А) до точки (В) получались разные результаты.
Решить данную проблему можно заменив ленту на заведомо исправную. Открыть в новой вкладке
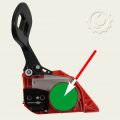 Рис.1 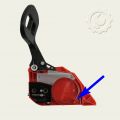 Рис.2 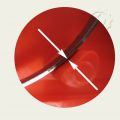 Рис.3 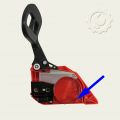 Рис.4 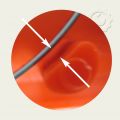 Рис.5 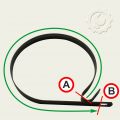 Рис.6
|
Цепь. Провисание (пила цепная бензиновая) Развернуть ▼
|
Появились случаи с неисправностью, которая проявляется в том, что при попытке перемещения цепи в ручную происходит периодическое провисание цепи (Рис.1). Т.е. такое ощущение что цепь движется по какому-то эксцентрику.
Проблема в неточности изготовления цепных барабанов, а иногда и цепных колес. В нашем конкретном случае был произведен замер цепного барабана на участке от касательной точки оси коленвала до выступа упора под цепное колесо (Рис.2_А). Результат замеров на Рис.3. Из полученных данных видно в точке А (Рис.3) сторона барабана имеет наименьший размер. В этой точке цепь будет провисать. И на оборот, в точке В (Рис.3) цепь будет натягиваться.
Иногда, дополнительно к этой проблеме может присутствовать кривизна коленвала. Измерить отклонения можно с помощью микрометра (Рис.4).
И на последок сама шина. Некачественное изготовление этого узла, также существенно влияет на провисание цепи. Иногда ведомая звездочка выполнена несоосно, вызывает неравномерное вращение. Цепь при этом может то натягиваться, то наоборот отпускаться. На Рис.5 и Рис.6 показаны замера выступающего зуба звездочки, на которые опирается цепь. В одном случае это 1,22 мм, повернув звездочку на 180 градусов, мы получаем уже 1,91 мм. Т.е. неравномерность натяжения цепи будет около 0,7 мм!
Замена на качественные комплектующие решат проблему. Такая неисправность относится к гарантийным случаям. Открыть в новой вкладке
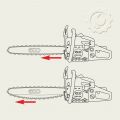 Рис.1 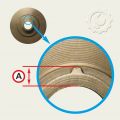 Рис.2 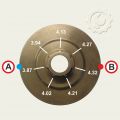 Рис.3 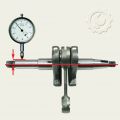 Рис.4 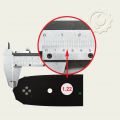 Рис.5 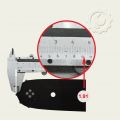 Рис.6
|
Карбюратор для любознательных. Для чего ''дырочки'' в диффузоре (2-х тактные двигатели) Развернуть ▼
|
Внутри диффузора, в зоне дроссельной заслонки (Рис.1), можно заметить 2 или 3 отверстия (Рис.2). Это каналы жиклеров холостого хода или байпас (от английского bypass — обход). Разобрав карбюратор и удалив заглушку с обратной стороны отверстий, можно заметить небольшую полость (Рис.3). Это так называемая камера холостого хода (КХХ). Речь пойдет о ней (Рис.4) и о том как это работает.
На Рис.5 давление перед дроссельной заслонкой (Р-красный цвет), после дроссельной заслонки (Р-оранжевый цвет), 1 и 2 - вторичные жиклеры ХХ, 3 - первичный жиклер ХХ. При неработающем двигателе давление перед дроссельной заслонкой (Рис.5_Р-красный цвет) и после (Рис.5_Р-оранжевый цвет) одинаково. При работающем двигателе давление после дроссельной заслонки (Рис.5_Р-оранжевый цвет) начинает падать. Из-за появившейся разницы давлений воздух начинает поступать во вторичные жиклеры (Рис.5_1,2), смешивается с топливом в камере ХХ и минуя дроссельную заслонку попадает через первичный жиклер ХХ (Рис.5_3) в камеру сгорания двигателя. Процесс режима холостого хода двигателя на Рис.6_GIF.
При нажатии на газ дроссельная заслонка перемещаясь, подключает к работе первичного жиклера холостого хода вторичный жиклер. Вторичный жиклер может быть один. Это применяется в устройствах не критичных к нагрузкам на приводном валу двигателя. В устройствах с существенными нагрузками на валу двигателя (бензорезы, цепные пилы, мотобуры и пр.) карбюраторы выполнены с дополнительными вторичными жиклерами (такой вариант мы и рассматриваем). Это объясняется промежуточным состоянием дроссельной заслонки - приоткрытое состояние. Это когда дроссельная заслонка приоткрыта, воздух поступает через нее, но главный топливный жиклер еще не задействован (не хватает достаточного разрежения). Получается временный "провал" оборотов двигателя, на какой-то момент в промежуточном состоянии обедняется смесь и двигатель как бы "душится". Избежать эту проблему помогают дополнительные жиклеры вторичного признака.
Как это происходит видно на Рис.7_GIF.
Открыть в новой вкладке
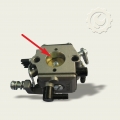 Рис.1 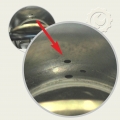 Рис.2 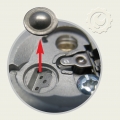 Рис.3 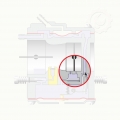 Рис.4 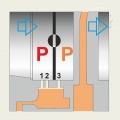 Рис.5 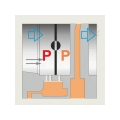 Рис.6_GIF 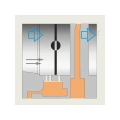 Рис.7_GIF
|
Карбюратор настройка - нюансы (2-х тактные двигатели) Развернуть ▼
|
Эта статья дополнение к основной "Карбюратор настройка (2-х тактные двигатели)".
В карбюраторах к 2-х тактным двигателям есть конструктивная особенность в подаче топлива к жиклерам. Их можно разделить на два типа. С независимой системой и с зависимой. Под независимой системой понимаются карбюраторы у которых полость с главным жиклером отделена от полости жиклеров холостого хода. Под зависимой системой топливоподачи следует понимать карбюраторы у которых эти полости объединены.
Общая подача топлива в карбюратор происходит через канал (Рис.1_А - синяя зона) и регулируется запирающей иглой (Рис.1_1). После иглы находится полость для обеспечения подачи топлива к жиклерам (Рис.1_В - зеленая зона). Эту полость можно условно сравнить с поплавковой камерой карбюраторов для 4-х тактных двигателей. Такое сравнение приведено для лучшего понимания принципа работы. По мере расходования топлива из этой камеры объем его уменьшается и мембрана (Рис.1_4) прогибается, нажимает на коромысло и иглой открывает канал для пополнения топлива. По аналогии мембрана играет роль поплавка в карбюраторах с таким механизмом. Объем топлива в этой полости обязан балансу между противодействующими силами. С одной стороны атмосферное давление пытается прогнуть мембрану и открыть иглой канал с топливом, с другой стороны пружина под коромыслом компенсирует это давление. Благодаря этому в полости находится определенное значение объема топлива. Как только топливо, по мере расхода, уменьшается, баланс нарушается. Атмосферное давление превышает внутреннее и мембрана, прогибаясь, открывает иглой канал с топливом.
Далее топливо, прежде чем попасть к жиклерам, дозируется регулировочными винтами. Винт количества смеси (Рис.1_2) регулирует подачу топлива к главному жиклеру. Винт качества смеси (Рис.1_3) регулирует подачу топлива к жиклерам холостого хода.
И вот тут о сути вопроса. На Рис.2 карбюратор с независимой системой подачи топлива. С мембранной полостью (Рис.2_А) полость главного жиклера (Рис.2_В) и полость жиклеров холостого хода (Рис.2_С) соединены независимо друг от друга. По этому изменение количества топлива при холостом ходе (ХХ) означает также изменение количества топлива при полной нагрузке. Если количество топлива при холостом ходе было изменено винтом "L" (Рис.1_3), то необходимо подрегулировать винт "Н" (Рис.1_2). Опасность заключается в том, что отрегулировав качество смеси мы можем получить обедненную смесь на полном газу. А это большие проблемы с ЦПГ!
На Рис.3 карбюратор с зависимой системой подачи топлива. Здесь полости главного жиклера и жиклера холостого хода объединены (Рис.3_С). В данном случае выше описанная проблема отсутствует. Как бы мы не изменяли количество топлива на жиклере ХХ это не повлияет на настройки главного жиклера.
Путь прохождения топлива с независимой системой подачи топлива (Рис.4) и путь прохождения топлива с зависимой системой (Рис.5) Открыть в новой вкладке
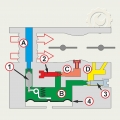 Рис.1 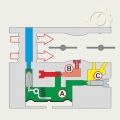 Рис.2 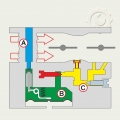 Рис.3 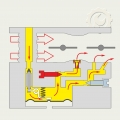 Рис.4 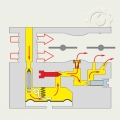 Рис.5
|
Тяга газа, выпадение (DGM_GS-282) Развернуть ▼
|
Были случаи, когда у новой бензопилы моделей DGM выпадала тяга газа (Рис.1). Причина неисправности - неправильная сборка инструмента на заводе либо при неквалифицированном ремонте.
На верхней накладке на рукоятку есть выступ (Рис.3), ограничивающий выпадение тяги. Выступ проходит рядом с тягой, прижимая ее к курку (Рис.2_2, желтая линия). В курке имеется два отверстия большое и маленькое (Рис.4). Большое отверстие предназначено для кнопки (с левой стороны рукоятки), которая должна блокировать курок газа в нажатом состоянии (режим холодного пуска). Если сборщик заправил тягу в это отверстие (Рис.4_1, красная), то кнопка-блокиратор вытолкнет ее из курка (Рис.2_1). При правильной установке тяги (Рис.4_2, синяя) этого не происходит. На Рис.5_2 видно как выступ перекрывает тягу от выпадения. Тяга (Рис.5_1) находится ниже выступа и в этом случае удержания тяги не произойдет. Более наглядно видно на схеме (Рис.6).
В некоторых случаях, из-за некачественного литья накладки (Рис.7_1) приходилось исправлять дефект. Для этого слегка разогревался участок с выступом феном и вставлялся клинышек (Рис.7_2). После остывания выступ принимает правильное положение. В качестве клинышка мы использовали алюминиевую проволоку диаметром в 5 мм.
И напоследок о винте крепления верхней накладки на рукоятку. Бывали случаи, когда на заводе вкручивался слишком длинный винт и чтобы он не вылез наружу через накладку, его немного не докручивали. В результате накладка болталась, что так же негативно сказывалось на позиционирование выступа относительно тяги газа. Винт должен быть не более 15 мм. Открыть в новой вкладке
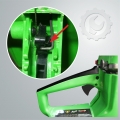 Рис.1 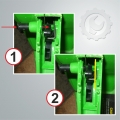 Рис.2 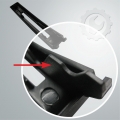 Рис.3  Рис.4 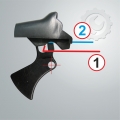 Рис.5 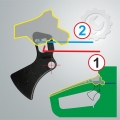 Рис.6 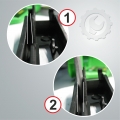 Рис.7 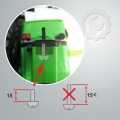 Рис.8
|
Поломка оси шкива стартера (цепная пила) Развернуть ▼
|
При диагностике обнаружена поломка оси шкива стартера в месте соединения её с корпусом стартера (см. фото).
Данная поломка вызвана наличием в этом месте внутренней полости в результате чего произошло снижение прочности конструкции. Образование этой полости является дефектом возникшим при изготовлении данной детали.
Денная поломка является гарантийным случаем и устраняется безвозмездно для владельца. Открыть в новой вкладке
|
Абразивный износ поршня (2-х тактный двигатель) Развернуть ▼
|
При диагностике обнаружен износ поршня, особенно сильный со стороны впускного окна (см. фото).
Данное повреждение вызвано попаданием абразивных частиц во впускной тракт двигателя (отсутствовал воздушный фильтр тонкой очистки).
В данном случае требуется замена цилиндра и поршня, а также проверка состояния остальных деталей ЦПГ. Ремонт проводится за счёт владельца инструмента, так как неисправность носит эксплуатационный характер и не является гарантийным случаем. Открыть в новой вкладке
|
Нет подачи масла на цепь (CSP-150) Развернуть ▼
|
Иногда масляный шланг переламывается пополам из-за тонких стенок трубки (Рис.1). Можно применить способ доработки узла, поместив масляную трубку в пружинку подходящего диаметра, тем самым создав ей каркас (Рис.2). Открыть в новой вкладке
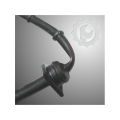 Рис.1  Рис.2
|
Самопроизвольное раскручивание винта картера (CSP-164) Развернуть ▼
|
В цепной пиле ECO CSP-164 появлялись случаи самопроизвольного откручивания винтов крепления картера. Головка, открутившегося винта, попадает под вращающийся маховик и как результат возможно разрушение корпуса картера, повреждение модуля зажигания или самого маховика. Рекомендуем проделать несложную профилактическую работу. Демонтируем маховик (Рис.1) и обращаем внимание на винты крепления картера (Рис.2). В нашем случае видим открутившийся винт (Рис.3), а на маховике след от головки винта (Рис.4). Откручиваем винт и садим его на фиксирующий состав для резьб. Данную процедуру рекомендуем провести даже в том случае если откручивания не обнаружено. Такая профилактика поможет избежать в последующем крупного повреждения. Открыть в новой вкладке
|
Кратко о свечах зажигания Развернуть ▼
|
Состояние свечи может о многом рассказать в работе двигателя. На картинках свечи работавшие в различных режимах работы двигателя. Рис.1 - цвет слегка рыжеватый, без налета, нормальное состояние свечи - правильная работа двигателя. Рис.2 - цвет черный с нагаром, двигатель работал на богатой смеси (много топлива, мало воздуха). Рис.3 - цвет белесый, двигатель работал на бедной смеси (много воздуха, мало топлива). Рис.4 - цвет ярко красноватый, в топливе присутствует много присадок. Все три последние свечи говорят о неудовлетворительной работе двигателя.
Для двухтактных двигателей самым опасным состоянием является обедненная топливо-воздушная смесь. Об этом подробно в статье "кратко о двухтактных двигателях". По бедной смеси (свеча Рис.3) проверяем либо откуда поступает лишний воздух, либо где не поступает топливо. В обоих случаях это приводит к бедной смеси.
Для сокращения времени на диагностику начинаем с простого и наиболее часто встречающегося. Проверяем топливный фильтр. Иногда его называют всасывающей головкой и это не случайно. Топливные фильтры в бензотехнике типа мотокос, цепных пил и пр. бывают разных типов, но во всех присутствует абсорбирующий элемент, который герметично связан с топливной трубкой. Это необходимо для того чтобы при кратковременном выпадании из зоны топливной смеси (от вибрации, при перевороте устройства, когда фильтр наполовину погружен в топливо) не подхватывался воздух. Бывали случаи когда элемент отсутствовал полностью.
Проверяем целостность топливного шланга. Далее - герметичность самого двигателя не разбирая его. Ослабляем винты крепления глушителя. Между глушителем и цилиндром вставляем подходящий кусок резины и поджимаем винты. Заворачиваем свечу. К карбюратору подсоединяем переходник со штуцером для компрессометра или просто ручного насоса (в последнем случае придется воспользоваться бочкой с водой). Т.е. получается что двигатель вместе с карбюратором имеет только одно отверстие наружу - это штуцер. Накачиваем и смотрим. С компрессометром по манометру, с насосом по пузырям в бочке. Этим мы сразу проверяем герметичность карбюратора, переходного колена между карбюратором и цилиндром, всех прокладок и наконец сальников коленвала. По результатам делаем вывод.
При богатой смеси (свеча Рис.2) проверяем чистоту и работоспособность карбюратора. Под работоспособностью подразумевается отсутствие заедания при перемещении или зависания иглы карбюратора. Про карбюратор есть отдельные статьи ("Карбюратор настройка _http://remont.tools.by/diagnostics/view/1583157826", "Карбюратор настройка - нюансы_http://remont.tools.by/diagnostics/view/1583412753", "Для чего ''дырочки'' в диффузоре_http://remont.tools.by/diagnostics/view/1583745422".
Чистоту топливного фильтра порой на глаз определить трудно. С виду чистый, а на практике не работает. Иногда пользователь может использовать некачественную смесь в которой растворен какой-то материал типа пластика, смол и пр. Это может быть неправильное хранение топлива (ПЭТ-бутылки, канистры из-под олифы и им подобное). После высыхания топлива, растворенный материал забивает абсорбирующий элемент и фильтр становится непригодным.
Отдельно стоит отметить свечи замасленные и мокрые. Это признак либо перелива большого количества топлива (зависание иглы карбюратора, неправильная настройка), либо отсутствия искры зажигания. Открыть в новой вкладке
|
Кратко о двухтактных двигателях Развернуть ▼
|
Двигатель внутреннего сгорания работает на топливо-воздушной смеси в соотношении 1:14,7. Это соотношение принимается как L=1. Уменьшение воздуха или увеличение топлива, поступаемого в двигатель, считается богатой смесью. И наоборот увеличение воздуха или уменьшение топлива в смеси считается бедной.
На Рис.1 график на котором видно в каких режимах двигатель еще будет работать (желтая, оранжевая,красная линии), а в каких он просто не заведется (синия линия). Это режимы где L<0,6 и L>1,35.На графике вертикальная ось координат - скорость фронта пламени. Чем выше скорость фронта пламени, тем выше обороты двигателя и короче продолжительность сгорания топлива. На температуру двигателя это влияет на прямую. Дольше продолжительность горения, меньше времени на охлаждение двигателя и на оборот. В режиме работы двигателя есть условно три зоны. Зона нормальной работы ДВС - "В". И две зоны работы ДВС в нежелательных режимах. Это на богатой смеси "А" и на бедной смеси "С".
Наиболее опасным режимом работы двухтактного двигателя является зона бедной смеси. В этом режиме сильно повышается температура горения при плохом охлаждении двигателя. Это приводит к срыву масляной пленки. В результате добавляется трение и температура мгновенно растет до состояния оплавления алюминия. Происходит задир поршневой группы и даже прогорание самого поршня Рис.2. Задир на поршне чаще всего образуется со стороны глушителя, что является характерным признаком работы на бедной смеси. Разрушение поршня от глушителя объясняется самой высокой температурой в этой области. Далее повреждение распространяется по всему радиусу поршня.
Задир поршня по всей поверхности (Рис.4) скорее говорит об отсутствии или недостаточном количестве масла в топливной смеси. Открыть в новой вкладке
|
|
|
|